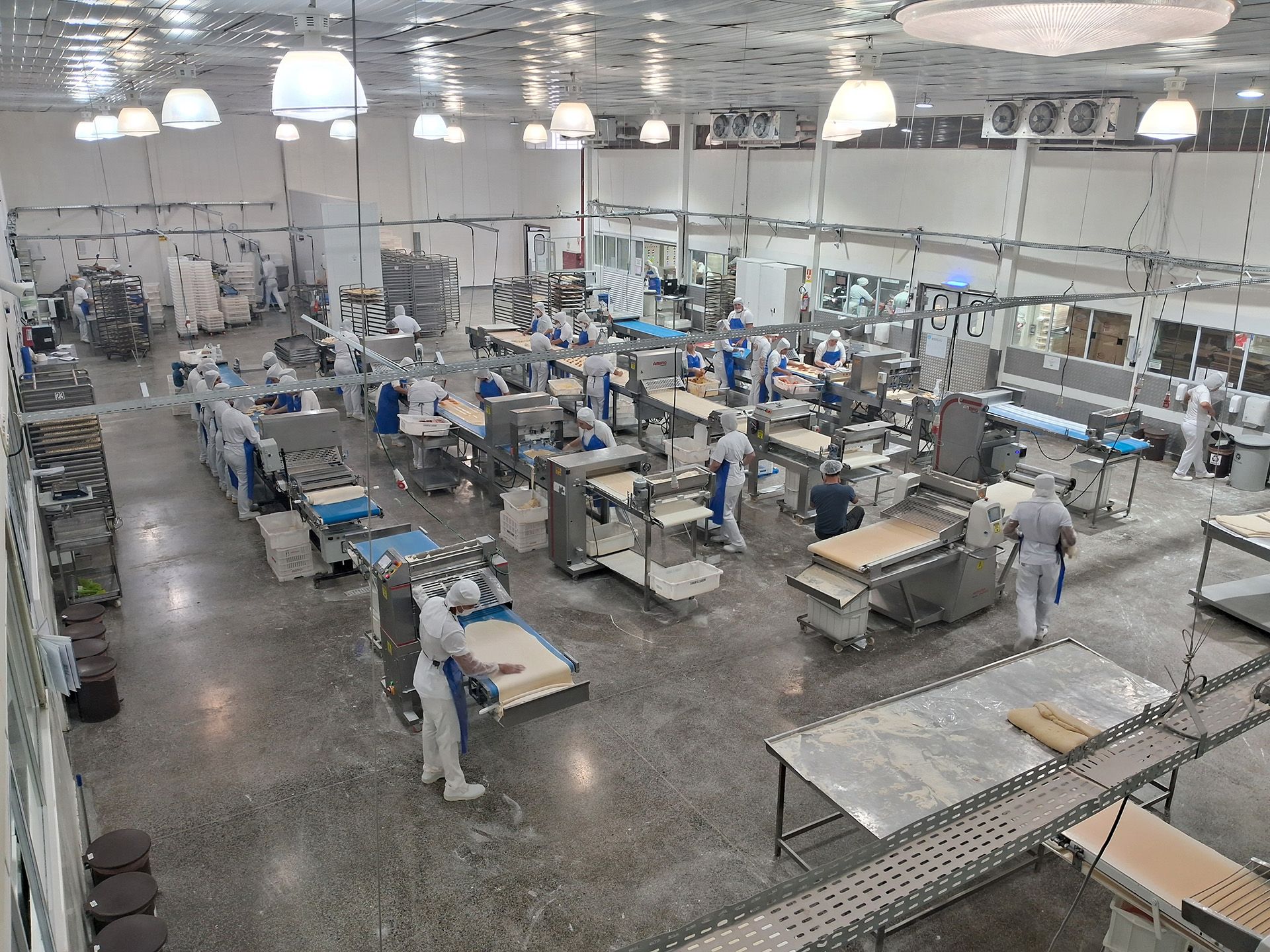
Paraná’s food industry automates processes with Full Gauge Controls technology
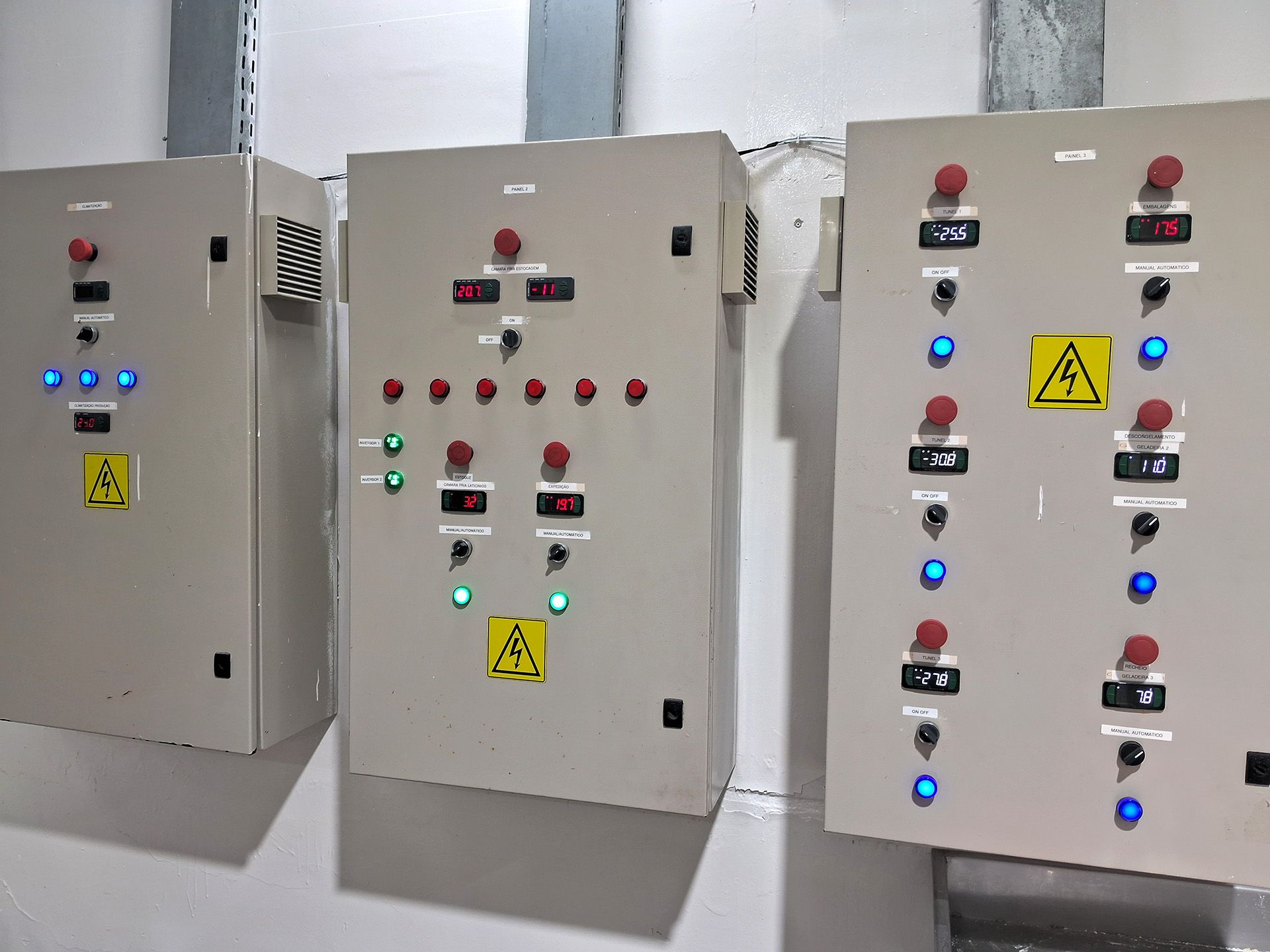
Paraná’s food industry automates processes with Full Gauge Controls technology
_Sabor&Sabor operates in six Brazilian states and ensured the quality of its products through the Sitrad PRO software. _
Sabor&Sabor, from Curitiba (Paraná), is the largest manufacturer of snacks and frozen foods in southern Brazil. With more tan 30 years in the market, the bakery operates an industrial facility with over 3.300 m² of building areas, and has found guarantees in the Full Gauge Controls controllers technology, together with the Sitrad PRO software, to keep the essence of handcrafted goods preparation of the recipes, up to the delivery to local distributors.
Sabor&Sabor uses the RCK-862 controllers to manage the reciprocating compressors, as well as the MT-512E Log and TC-900E Log models for the cooled and frozen goods chambers, respectively. “We have eight compressors ruled by the RCK-862; three freezing tunnels; a frozen goods stockpile chamber; three climatization areas; one chiller and three cooled goods chambers”, details the industrial maintenance supervisor, André Rui da Silva. And al lof them are connected to Sitrad PRO, which allows us to remotely manage them, and offers faster routines for the maintenance technician. “The installation of Sitrad PRO was the key factor to remotely manage the machine room operations. This enabled me to save time and the decision-making process” he states. According to Andre, automating processes with Sitrad PRO was essential to act and react in a real-time manner, which shows the tech’s benefits, developed back in 1997 by Full Gauge Controls, and is constantly being updated to contribute to the refrigeration technicians’ day-to-day tasks.
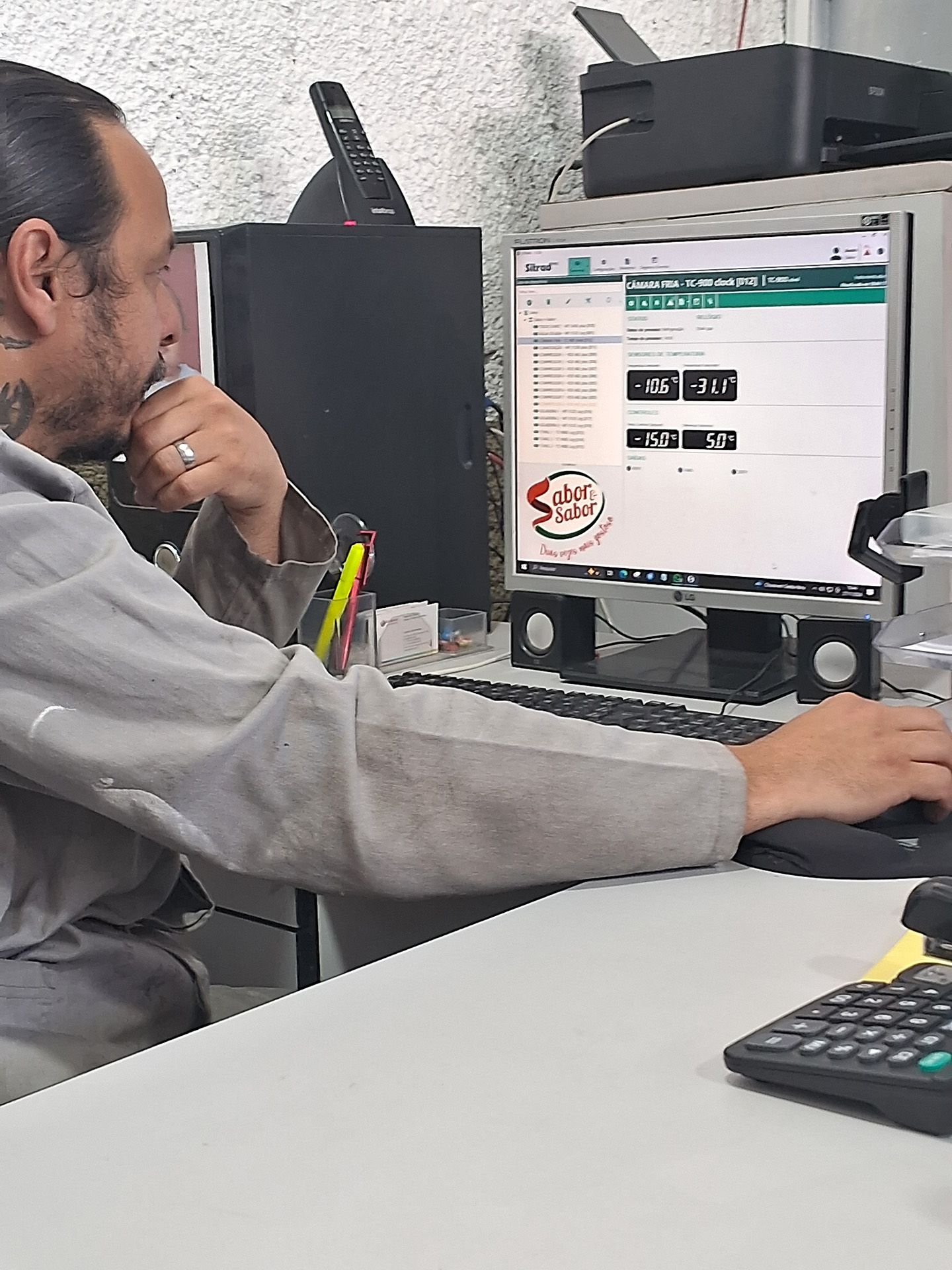
The relationship between Sabor&Sabor and Full Gauge Controls started even before the supervisor was a part of the team. André, who has been with the company for five years, mentions that the bakery was already using Full Gauge Controls’ controllers, but it was from the moment of installing the first RCK-862 when the automation of more complex processes was enabled. “We were using PLCs that were revamped and became significantly more expensive, so we looked for options with the best cost-benefit ratio. After an extensive analysis, the RCK-862 was chosen as the best alternative, including its post-sale support, which helped us to develop the recipes since there was no history of using these kinds of controllers in large compressors (30 and 40 HP), especially with the use of the Variable Speed Compressor Control function using anhydrous ammonia,” André explains.
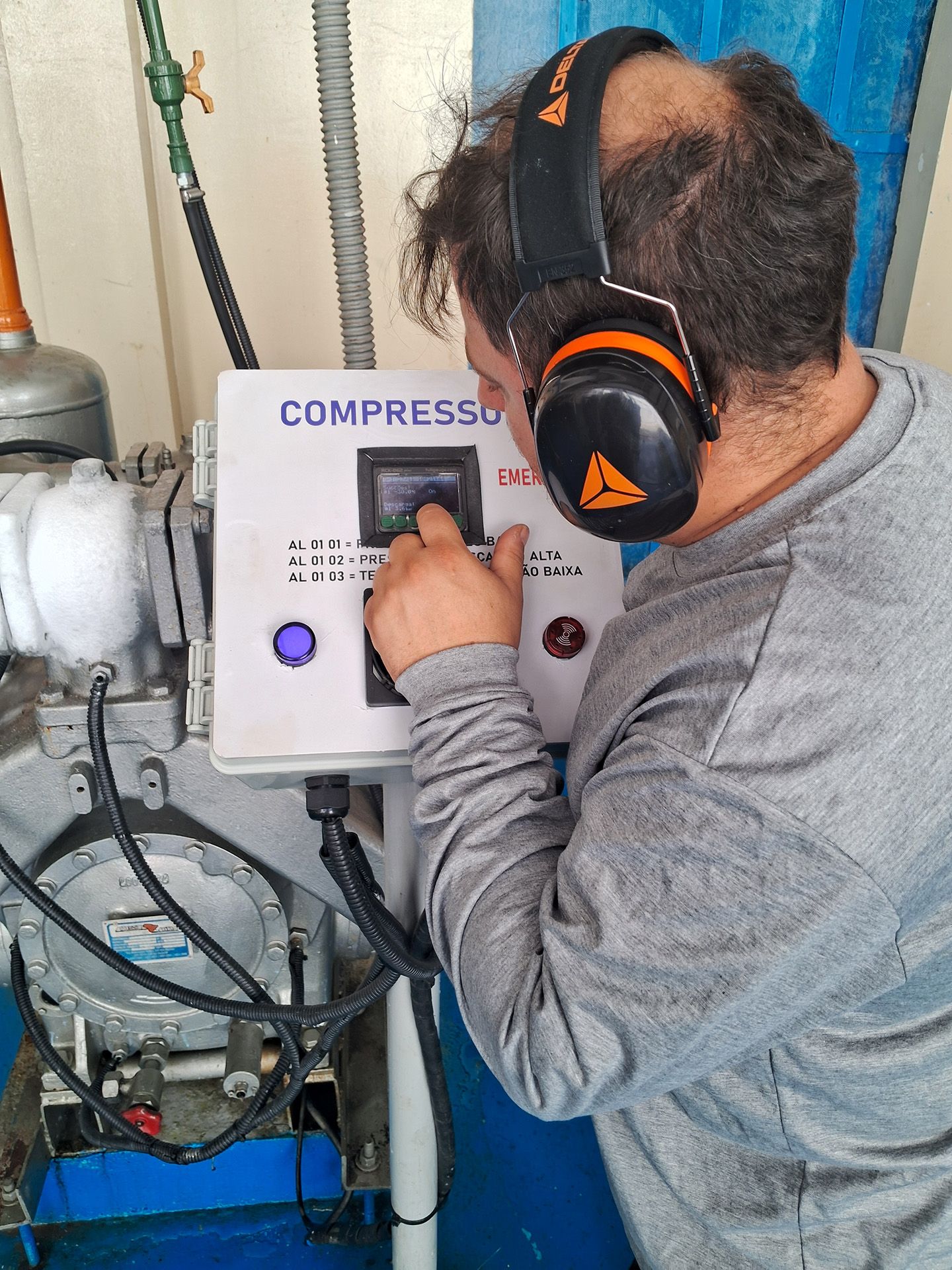
Furthermore, André highlights the intuitive potential of Full Gauge Controls’ solutions, which aim to obtain energy efficiency. “Everything was so easy and intuitive that in one day I installed and set up everything, even the process automation macros such as defrost, setpoints and on/off. With this, we optimized the facility, and we are saving energy,” he mentions.
Would you like to know more about Full Gauge Controls’ solutions? Click on: www.fullgauge.com and www.sitrad.com