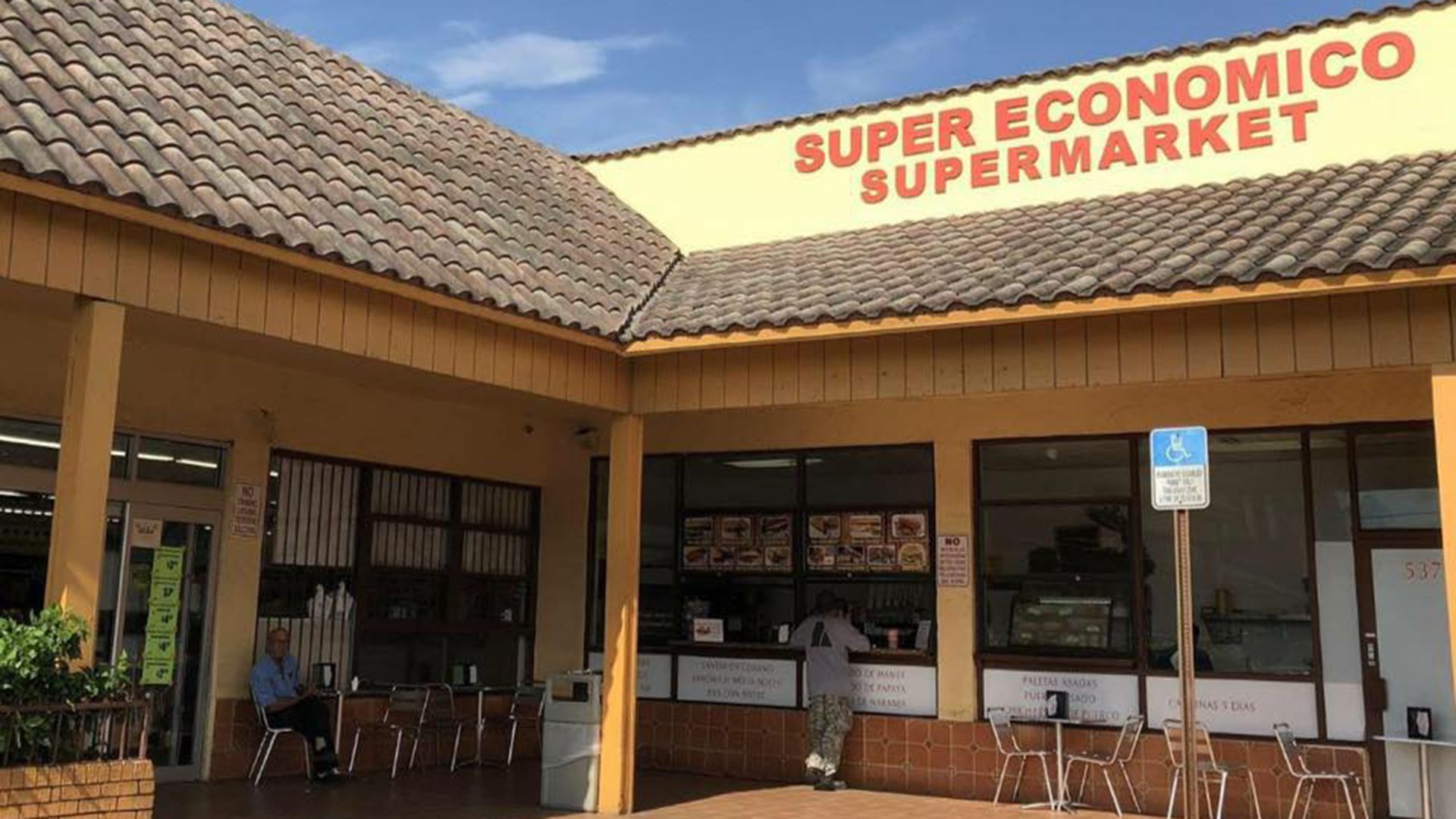
Remote monitoring reduces to 100% product loss in ice cream freezer
Remote monitoring reduces to 100% product loss in ice cream freezer
Precise temperature control is fundamentally relevant to maintain quality and integrity of temperature sensitive products, avoiding product loss and extending shelf life. It also plays a crucial role to improve energy efficiency leading to optimization of operating cost and maintenance.
A case study was made on an independent supermarket that had an ice cream freezer with continuous problems, where the product kept losing its consistency, changing the quality and texture, causing product loss.
At first it was not possible to determine exactly why the freezer did not reach the desired temperature during business hours, preventing the product loss. Even after the defrost process ended the ambient temperature did not drop to the point of satisfying the temperature of the product to remain frozen.
After some technical calls were made, and still it was not possible to determine the cause of failure, extending the problem for weeks it was decided to improve the accuracy of the temperature control and defrosting process, the customer seek the adoption of an electronic controller, in replacement of the old mechanical thermostat and defrost timer.
Thus, the TC-900E Log controller was selected for the application. This controller has an integrated datalogger and communication with Sitrad management software, which enables constant monitoring of operating temperatures and status of the control outputs, in addition to offering graphical and text reports from the stored data.
After only a few hours of service, Sitrad PRO, through graphic reports, assisted the technician to identify that the defrost heater was not sufficiently capable of performing a complete defrost, requiring the exchange of defrost heater to one of greater capacity. In addition, the TC-900E Log datalloger when storing 24 hours of data and sending it to Sitrad PRO, showed the business owner a strategic operational mistake when loading products in the freezer.
The loading process was taking place immediately after the defrost process was completed, where the freezer room temperature was at its highest. When the doors were opened for loading product, the temperature rose even more, with no time to normalize it prior to the business opening hours. Advancing through normal operating hours, consumers found the product softened and unsuitable for consumption. The monitoring and control of the TC-900E Log, in conjunction with Sitrad PRO software, revealed the origin of the problem and brought to light improvements in just a brief time of operation.
Sitrad PRO continuously follows the process of monitoring and control, generating reports and, when necessary, sending alerts to the managers of this business via cell phone, through Sitrad Mobile, in case this freezer again presents temperatures that are harmful to the product or for the equipment itself, saving not only money in the matter of additional costs in maintenance or energy, but also time because of the remote technology.